8D-Report
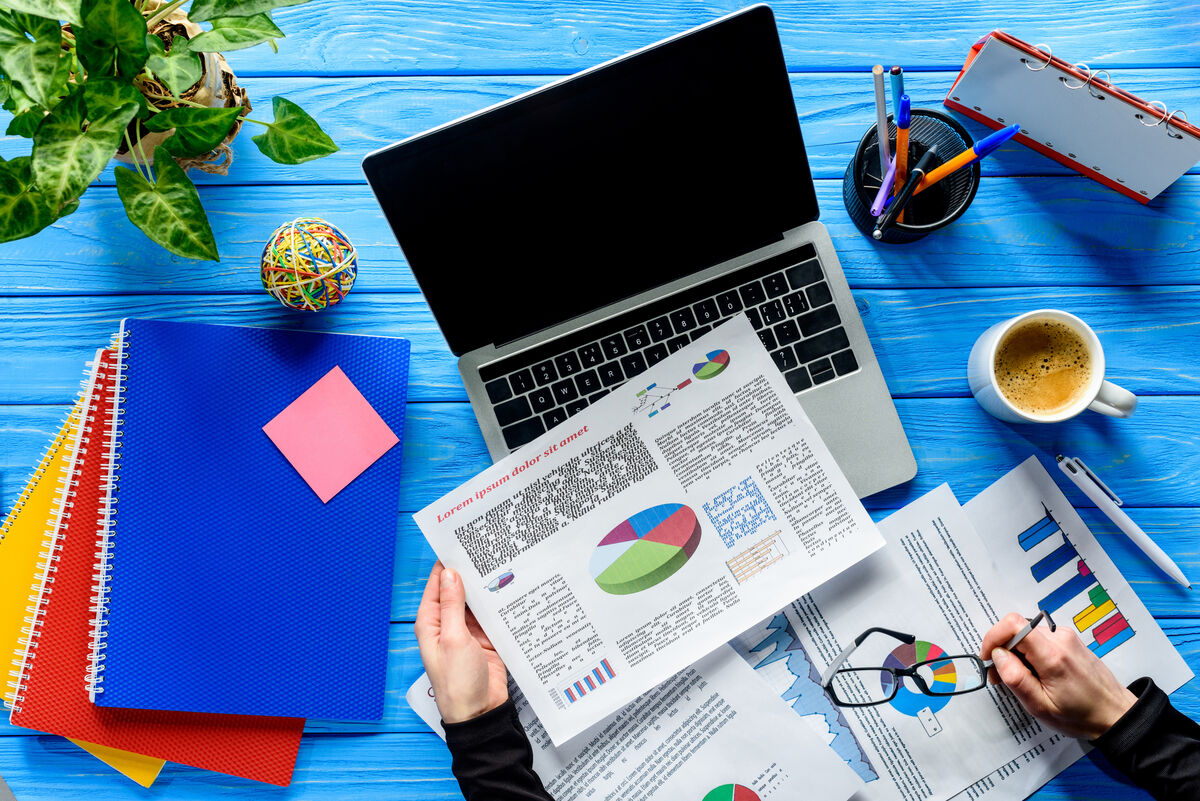
(Quelle: VadimVasenin - depositphotos.com)
1. Executive Summary
Der 8D-Report ist das Dokument, das die Ergebnisse einer Problemlösung nach der 8D-Methode dokumentiert. Wenn eine Reklamation oder ein Problem gemeldet werden, erfolgt zunächst eine klare und vollständige Beschreibung und Eingrenzung des Problems. Danach werden Sofortmaßnahmen eingeleitet, die dafür sorgen, dass der Kunde mit dem Problem nicht mehr konfrontiert ist. Nach einer Ursachenanalyse werden Maßnahmen zur Korrektur des Fehlers entwickelt. Diese müssen auf ihre Wirksamkeit geprüft und anschließend im Unternehmen verankert werden. Nach Abschluss der Problemlösung sind die gewonnenen Erkenntnisse sowohl für andere bestehende als auch für zukünftige Produkte verfügbar zu machen.
2. Definition
Der 8D-Report ist das Dokument, das die Ergebnisse einer Problemlösung (ausgelöst durch eine Reklamation) nach der 8D-Methode dokumentiert. Der 8D-Report ist ein Element des Reklamationsmanagements und somit Teil des Qualitätsmanagements. Aber auch in den Bereichen Arbeitsschutz und Umweltschutz wird der Report verwendet. 8D steht dabei für die acht obligatorischen Disziplinen (Prozessschritte), die bei der Abarbeitung einer Reklamation erforderlich sind, um das zu Grunde liegende Problem zu überwinden.
3. Ziele und Nutzen
- Fehlerkosten sollen deutlich miniert werden. Insbesondere gilt es hier, Kosten, die aus Garantiefällen oder auch Kulanzfällen entstehen, zu reduzieren.
- Steigerung und Sicherstellung der Qualität von Produkten und Dienstleistungen.
- Durch die Einsparung von Kosten und der Optimierung von Prozessen und Entwicklungsabläufen soll der Gewinn gesteigert werden.
- Professionelle Reaktion auf Kundenreklamationen.
4. Anwendung
- 8D kommt bei Problemen zur Anwendung, die neben der nachhaltigen Problembeseitigung auch Sofortmaßnahmen erfordern.
- Eingesetzt wird 8D am häufigsten zur Abarbeitung von Kundenreklamationen.
- Das Verfahren ist aber ebenso für andere unerwünschte Situationen, die Sofortmaßnahmen erfordern, sehr gut einsetzbar. Beispiele dafür sind auftretende Probleme im Rahmen der Produkterprobung, ungeplante Anlagenstillstände in der Produktion oder Arbeitsunfälle.
5. Vorteile und Grenzen
5.1 Vorteile
- Schnelles Erkennen von Problemursachen, da sich die Anwender intensiv mit der Problemstellung auseinandersetzen müssen und durch die Struktur des Formulars durch den Bogen geführt werden.
- Effektiver Ansatz zum Finden einer Grundursache, zum Einleiten von Abstellmaßnahmen, um Grundursachen zu eliminieren, und zum Implementieren von permanenten Abstellmaßnahmen.
- Hilft, das Kontrollsystem zu erforschen, welches dem Problem den Ausbruch ermöglichte. Der Ausbruchspunkt wird analysiert, mit dem Ziel, die Leistungsfähigkeit des Kontrollsystems zu verbessern, um den Fehler oder die Ursache bei erneutem Auftreten zu entdecken.
5.2 Grenzen
- Zeitaufwändig aufgrund einzuhaltender Struktur
- Personalaufwändig, durch eingebundenes Team
- Gefahr der "schnellen Aktionen" (durch die Ungeduld der Betroffenen)
- Mögliche Komplexität der Wirksamkeitsprüfung in D5 und D6
- Die Entwicklung von 8D-Training kann zeitraubend und schwierig sein.
- Erfordert sowohl Training im 8D-Problemlösungsprozess als auch Datenerfassungs- und Datenanalysetools, wie z.B. Pareto-Diagramme, Fischgrätendiagramme und Ablaufdiagramme.
6. Erstellung, Ablauf und Bearbeitungsdauer
6.1 Erstellung und Ablauf
Um die Problemlösungsarbeit zu unterstützen, empfiehlt sich die Einführung einer 8D-Roadmap als Leitfaden zur Problemlösung.
Zugeordnet zu den acht Schritten zeigt sie die Hauptaufgaben, häufig verwendete Werkzeuge und die erforderlichen Ergebnisse.
Abb.1: 8D-Roadmap
Schritt D1: Team bilden
- Ist ein Problem erkannt, wird ein Teamleiter benannt und ein Team zusammengestellt.
Schritt D2: Problem beschreiben
- Problem so vollständig und präzise wie möglich beschrieben werden
- Erfassung der Abweichung des Ist- vom Soll-Zustand
- In D2 gilt es noch nicht, die Frage nach der Ursache zu klären; das geschieht im vierten Schritt.
- Zur Erfassung des Fehlers in Form von Zahlen und Fakten dienen z. B. die Fehlersammelkarte, das Histogramm und das Pareto-Diagramm.
Schritt D3: Sofortmaßnahmen treffen
- Die Umsetzung der Sofortmaßnahmen dient dazu, akuten Schaden vom Kunden und dem eigenen Unternehmen abzuwenden.
- Die Wirksamkeit der eingeführten Sofortmaßnahmen muss sichergestellt werden, bis geeignete Abstellmaßnahmen eingeführt wurden (D6).
- Geeignete Sofortmaßnahmen können Ersatzlieferungen, Reparatur, Gutschriften, das Aussortieren von fehlerverdächtigem Material mit anschließender 100%-Prüfung oder sogar der zeitweise Stopp der Produktion sein.
Schritt D4: Ursachen analysieren
- Überblick über die möglichen Ursachen des Problems verschaffen.
- Mögliche Ursachen für den Fehler identifizieren und geeignet darstellen.
- Hilfsmittel: Ursache-Wirkungs-Diagramms oder einer Mindmap.
- Anschließend sind die Kernursachen zu identifizieren und deren Einfluss auf das Problem darzustellen.
Schritt 5: Abstellmaßnahmen festlegen (inkl. Wirksamkeitsprüfung)
- Ziel: ausgehend von den identifizierten Kernursachen geeignete Abstellmaßnahmen entwickeln und deren Wirksamkeit nachweisen.
- Mithilfe einer Wirksamkeitsprüfung ist nachzuweisen, dass durch die Abstellmaßnahmen das in Schritt D2 beschriebene Probleme vollständig beseitigt ist.
- Geeignete Maßnahme könnte sein: Veränderungen in der Produktion, wie z.B. die Verwendung besser geeigneter Werkzeuge sein.
Schritt 6: Abstellmaßnahmen organisatorisch verankern
- Vorgabedokumente entsprechend aktualisieren. Dies betrifft z. B. Arbeits- und Prüfanweisungen, Control Plans, Schulungspläne oder Instandhaltungspläne.
- Nach erfolgreicher Einführung der Abstellmaßnahme(n) wird/werden die Sofortmaßnahme(n) aufgehoben.
Schritt 7: Vorbeugungsmaßnahmen treffen
- Ziel: die gewonnenen Erkenntnisse für andere bereits bestehende und auch für zukünftige Produkte bzw. Prozesse verfügbar machen.
- Wirksamkeit der getroffenen Abstellmaßnahmen wird durch vermehrte Prüfung über einen längeren Zeitraum nachgewiesen (Erfolgskontrolle).
Schritt 8: Problemlösungsprozess abschließen
- Der Teamleiter muss sich davon überzeugen, dass alle im Rahmen des Problemlösungsprozesses vereinbarten Maßnahmen umgesetzt sind.
6.2 Bearbeitungsdauer
- Die ersten vier Schritte des 8D-Prozesses sollten innerhalb von vier Tagen abgeschlossen sein,
- der gesamte Prozess innerhalb von zehn Tagen.
7. Zuordnung greenQuality-Portfolio
- 2030101_Home_of_Quality
- 2030103_Home_of_Process
- 2030202_Home_of_Safety
- 2030203_Home_of_Environment_Protection
gQ-Knowledge-Owner
- Georg Flammersberger
8. Quellen
- https://www.qz-online.de/qualitaets-management/qm-basics/kunden/beschwerdemanagement/artikel/8d-sys tematisch-probleme-loesen-266317.html
- https://www.quality.de/lexikon/8d-report/#D6_Einfuehren_der_Abstellmassnahmen
- https://www.boehme-weihs.de/q-blog/caq-wissen/8d-report/
- https://www.qz-online.de/qualitaets-management/qm-basics/kunden/beschwerdemanagement/artikel/8d-systematisch-probleme-loesen-266317.html?_req_id=91607072386338:0FB096DFDE3B6584574BAD9D8D570F2C0E936467&article.page=3&survey_266317.current-step=1
Fordern Sie Ihre Unterlagen zum Thema an!
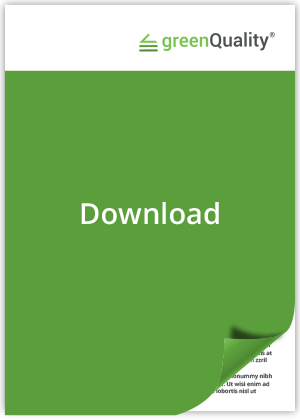
Teilen Sie uns in den nebenstehenden Feldern Ihre Kontaktinformationen mit, und Sie erhalten umgehend per Mail unsere weiterführenden Unterlagen zum Blogthema in digitaler Form.
Wir bedanken uns herzlich für Ihr Interesse an greenQuality und unseren Themen!